激光加工优势渐显 机遇与挑战共存
激光自问世至今已渗透至各行各业,先进的技术和独特的优势在各领域发挥着重要作用。近年来,在工业加工行业的表现尤为突出。作为20世纪重大发明之一,激光技术和激光产业的发展受到世界先进国家的高度重视,激光加工已成为对传统产业改造的重要手段。激光专家、中国激光加工委员会主任邓树森预测,今后2-3年内,我国激光加工设备销售额将会由2004年的15亿人民币上升翻一倍,达到30亿元的产值。
激光加工优势凸显 传统行业面临挑战
激光加工是继机械加工、力加工、火焰加工和电加工之后一种崭新的加工技术。它可以完善周到的解决不同材料的加工、成型和精炼等技术问题。从最小结构的计算机芯片到超大型飞机和舰船,激光加工都将是不可或缺的重要手段。
与传统的加工方法相比,具有能量最大限度地集中、易于操作、高的柔性、高效率、高质量、节能环保等突出优点,迅速在汽车、电子、航空航天、机械、冶金、铁路、船舶等工业部门广泛应用,几乎包括了国民经济的所有领域,被誉为“制造系统共同的加工手段”。
激光加工工艺包括:激光快速成形、激光焊接、激光打孔、激光切割、激光打标、激光去重平衡、激光蚀刻、激光微调、激光存储、激光划线、激光清洗、激光热处理、微加工和表面处理。与计算机数控技术相结合,激光加工技术已成为工业生产自动化的关键技术,拥有普通加工技术无法比拟的优势,逐步克服一些加工过程中传统工艺所遭遇的困难,开创了新的加工领域。
加工制造业是激光应用最基本、最深入的领域,例如在汽车制造业,从样车的开发、零部件的制造到车身总装的汽车生产,激光无所不在。在样车的开发和小批量试生产时,高度柔性的激光三维切割取代冲孔和修边模具,不仅节省模具,同时新车型的开发周期从传统方法研制开发一代新车5~7年的时间缩短为7个月。由于激光良好的可达性,使得汽车设计师可以自由地发挥其想象力和创造性,设计出独特风格的车型。
在车身总装上,激光焊接取代了电阻点焊工艺显示出有更高的效率、更优异的性能等。汽车工业在应用激光制造组装生产线后,可达到每57秒组装一辆汽车,一天组装1440辆的高速度,并且质量过硬。由于激光制造技术所具有的无与伦比的优势,在欧洲,几乎所有汽车制造厂在汽车研制开发和生产中无一例外的大量采用激光加工。
又如激光覆层是一项先进的焊接覆层技术,它能够修复金属部件的功能表面,与其它表面加工工艺相比,具有明显的优势,整个加工过程只需很少的热量消耗。
新技术日新月异 光纤激光器成热点
激光加工技术从最初的Nd:YAG激光器、CO2激光器,发展到大功率二极管模块、半导体泵浦全固态激光器、光纤激光器、飞秒激光器等各种新兴技术。其中,尤其以光纤激光器最为关注。传统激光行业中的大部分主要厂商都在2007年宣布进军光纤激光器市场,有的甚至推出了具体产品,这堪称是2007年度行业内发生的一个重大事件。
笔者今年参加国内多个激光展,如慕尼黑上海激光展、东莞激光展、武汉光博会上发现,其最显著的一个特征就是:新型光纤激光器的引入,以及传统激光器制造商开始进军光纤激光器市场。尤其在今年慕尼黑上海激光展上,各个主要厂商携带自己的光纤激光器产品悉数登场。
知名的光纤激光器供应商英国SPI激光有限公司中国首席代表陆明博士在接受记者采访时表示:“现在很多客户向我们询问采用光纤激光来进行激光切割的事宜,相对传统加工方式,激光切割质量好,效率高,在钣金加工领域是一种趋势,目前来看,随着环保、人工成本等考量因素逐步引起人们的关注,传统的加工技术已经不适应时代的发展,而激光加工这一高端技术也不仅仅用于高精尖加工制造领域,现在我们发现激光加工已经开始渗透到其他普通行业,如传统液晶显示器行业中的ITO膜采用化学腐蚀的方法来刻蚀,不但效率低,而且污染大,不利于环保,迫切需要新的替代解决方案,我们预计2009-2015年用激光来加工ITO膜将成为一种趋势,到2015年将彻底占领这个市场。”
目前进入该领域的企业有IPG、SPI、Trumpf、Newport、GSI、Rofin等国外大厂,却鲜有中国企业的身影,这种现象并不仅存在光纤激光器领域,在几乎所有主力激光器方面,国内激光设备厂商所采用的中高端激光器大部分依赖进口或国外厂家,这不得不令人扼腕叹息。
政府支持 产业转型将带动激光加工产业巨大发展
与国际上激光加工系统相比,我国的激光加工系统也差距甚大,仅占全球销售额的2%左右。主要表现为:高档激光加工系统很少,甚至没有;主力激光器不过关;微细激光加工装备缺口较大;不过这些领域我国的生产企业正在积蓄力量稳步进入,国内应用市场有很大发展空间。
希望:
首先,激光加工是一门21世纪发展极快的制造新技术,各国政府和工业部门都非常重视激光器和激光加工技术设备的发展。中国政府一直将激光作为“先进制造技术”列为国家重点发展项目。
国家重视,各级政府部门都在积极关注、规划、立项,多方面资金正在注入。特别是国家强调立项主体由大专院校,科研部门料转到以企业为主,这就促进了企业产品的自主创新,技术升级。
其次,受到国家节能减排、劳动力成本上升等因素的影响,国内许多传统产业急需业务转型,需要新的技术和设备来提升生产效率和质量,激光加工技术将会得到他们的青睐,来帮助他们增加产品技术含量,加快产品更新换代,满足市场对“个性化”产品的要求。
挑战:
产学研依旧配合不完善,自主创新力度欠缺
以半导体激光器核心技术为例,目前美国掌握着关键技术,德国由于有很大的应用市场(如汽车制造),现在也在迎头赶上,而目前中国在这方面正处于研发阶段,所生产的产品大部分集中在中低端市场。但是中国的应用市场近年来发展很快,目前发展速度是国外的2倍,但在自主生产方面几乎是空白。
当然国家投入也很多(自863计划开始),但收获很小,目前基本上靠进口。这其中还受到军事进口方面的限制,当然民用进口的没问题。中国的激光器产业未能有效作大,我们认为是产品的产业化过程出现了问题,一个产品在实验室研制出来了,但无法大规模生产,商用,无法产业化,即使制造出来了,也需要进行大量的试验测试,来验证其可靠性和稳定性,但这需要花费大量时间,有时候需要1-2年,这期间,产品或许已经过时。
随着中国改革开放程度日益增加,国外产品的大量涌入,未来国内激光器产业就更难发展了,这方面需要引起我们的关注。
缺乏行业标准 产品同质化严重
目前国内激光还处于“春秋战国”时代,比较混乱,行业里还没有一个比较规范的标准出台,包括各个产品的命名也很混乱。许多企业都是组装型公司,产品同质化严重,没有自己的核心技术,这些都严重威胁了中国激光产业在未来的健康发展。
国际大厂不断在中国投资建厂,形成国际竞争国内化等,这些都将对国内激光产业的发展产生一定的影响。
希望与挑战并存
目前,国内已逐步形成了产业群体激光零部件配套企业慢慢补齐,各类具有特色的激光加工系统制造商纷纷建立,国内已形成四个激光加工装备制造的产业带,它们主要分布在华中;珠江三角洲;长江三角洲和京津环渤海经济发达地区。国内生产经营激光加工设备的著名厂家有大族激光、上海团结普瑞玛、法利莱、光大激光、奔腾楚天激光、奥华激光、大族激光、金运激光、华工科技、粤铭激光等。
随着中国经济快速发展和国内经济的转型,激光加工技术必将逐步取传统加工技术,渗透到工业各个领域,中国也将迅速成为全球激光器和激光加工设备应用的重要市场,也将会产生世界级的企业。面对日益增长的巨大的激光加工应用市场和国际竞争新格局,中国的激光器和激光加工技术产业必将有一个大的发展,这种状况给国内外从事激光、激光加工技术设备研发、生产和经营的企业和投资者带来很大的机遇和挑战。(文:于占涛 wenjing)
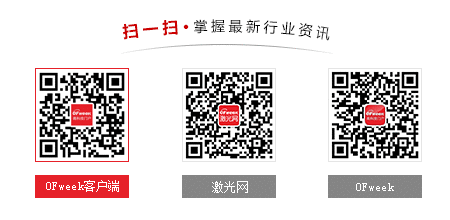
图片新闻
最新活动更多
-
限时免费立即试用>> 燧石技术,赋光智慧,超越感知
-
7月30-31日报名参会>>> 全数会2025中国激光产业高质量发展峰会
-
7.30-8.1马上报名>>> 【展会】全数会 2025先进激光及工业光电展
-
精彩回顾立即查看>> 筑梦启光 砺行致远 | 新天激光数字化产研基地奠基仪式
-
精彩回顾立即查看>> 抗冻不流汗——锐科激光『智能自冷却激光器』重磅发布
-
精彩回顾立即查看>> 宾采尔激光焊接领域一站式应用方案在线研讨会
推荐专题
发表评论
请输入评论内容...
请输入评论/评论长度6~500个字
暂无评论
暂无评论