无损检测在增材制造技术中应用的研究进展
3.增材制造技术的无损检测需求
增材制造的工件通常是一次性的,并且制造成本极其昂贵,因此传统的破坏性试验通常无法用于增材制造工件的检测。同时,由于增材制造工件是一层层创建的,属性更加难以预测,这就对增材制造工件的质量检测提出了挑战。从某种意义上来说,无损检测可以在不破坏工件完整性和服务性能的条件下完成对工件的质量评估,可以满足增材制造工件的独特检验要求。
全过程检测要求将无损检测方法用于增材制造过程中熔融状态下金属材料的表征,这远比制备好的工件检测难度大,同时要求检测过程不能干涉增材制造的加工过程。增材制造设备和工艺中需采用改进的无损检测传感器和控制器以提高检测和控制能力,提供实时的可见性并调节制造环境。在沉积过程中的实时检测和材料性能的确定,需能够提高合格零件的生产,使得增材制造生产的零件可以直接用于安装。
为了提高增材制造的工件质量,可能需要对整个系统实行闭环过程控制,例如能够逐层监控零件并控制或减轻零件的扭曲和残余应力,同时为每个增材制造工件提供详细的生成记录。过程控制也可以扩展到制造之前的原料,并验证零件的微观结构、几何形状和质量。由于在制造过程中,工艺参数偏离其最佳值可能会导致所加工工件的服役性能恶化,所以需要通过无损检测结果对增材制造工艺参数进行评价,评价的主要参数例如:声发射方法计算的系统偏差和光学传感器来确定的熔池深度。
针对材料的无损评价主要有五个方面的需求:原料无损检测、完成工件无损检测、缺陷影响监测、设计产品数据库和物理参数参考标准。原料无损检测,例如金属粉末尺寸、颗粒形状、微观结构、形态、化学成分分子和原子组成,这些参数需要被量化并最终评价其性能一致性;完成工件无损检测包括制造工件(无需进一步处理)和后处理工件(需进一步处理),检测内容包括小尺寸孔隙、复杂工件几何形状和复杂的内部特征;缺陷影响,用无损检测方法对完成工件中缺陷类型、产生频率和尺寸进行表征,便于理解产品属性对于产品质量和性能的影响;设计产品数据库,一个微观结构数据库可以编译阐明过程结构与性能之间的关系,包括每个过程中收集的图片或者照片,例如输入材料特性、原位过程监测及制造和后处理后完成生成的特征等;物理参数参考标准,目前缺乏合适的全尺寸工件来评价增材过程中的无损检测方法的可行性,由于增材制造的零件几何形状复杂、有嵌入较深的缺陷、有不同的微观结构(均与锻造相比),无损检测必须创建校验仪器的物理参考标准。
在增材制造过程中,需要对可能产生的缺陷进行实时监测,需要克服表面形貌和制备温度的影响,需要无损检测技术与制造过程进行集成而不影响增材制造工艺;加工完成的零件需要在验收阶段和使用寿命期间进行评估,确定其服役性能。此外,在零件的整个生命周期中,需要表征材料的微结构和形态,对原子和分子进行精细测量,表征内部应力状态等。总之,及时可靠的检测不同性质的缺陷和监测这些缺陷如何发展对于增材制造工艺具有重要的意义。因此,采用无损检测方法需要满足材料、设计以及测试需求,能够用于材料的全寿命周期,包括制造过程中优化、实施过程检测、生产后的质量验收以及服役过程中的质量监测。因此,增材制造的各个阶段对于无损检测都有明确的需求。
4.增材制造技术中无损检测技术的发展
目前在无损检测方面的技术主要包括:计算机断层扫描、渗透测试、涡流检测、超声检测和红外相机测量。如图4所示是一种采用声发射方式监测3D打印的实验系统。
X射线检测在工业上有着广泛的应用,无疑可以用来检测增材制造零件的孔隙率、尺寸误差和其他缺陷。X射线入射角直接影响检测缺陷的大小和形状,可以显示小于2%的样品厚度的缺陷。计算机断层扫描可以对所有样品进行检测,而超声检测和渗透检测是针对工件表面。X射线计算机断层扫描具有检测内部缺陷和内部特征的能力,可检测封闭孔和高密度夹杂物。同时,计算机断层扫描检测技术也具有一定的局限性,例如X射线的容积效应明显。同时,由于不能检测到垂直于X射线束的裂纹,导致其不能可靠的检测缺陷。总体而言,X射线计算机断层扫描是一种强大的对增材制成品进行无损检测的技术,使得描述材料的结构、形状分布和缺陷的定量尺寸成为可能。
增材制造的一个突出特点是比传统的锻造、铸造或模具成型零件具有更高的孔隙率,在这些零件中呈现不规则的粗糙表面,使得检测表面缺陷的传统无损检测方法难以应用。渗透检测为表面检测技术,检测固体材料及其制件的表面与近表面缺陷,用于检测不经过加工和抛光的多孔或者粗糙工件,难度较大,测量位置较深的复杂的内部结构或者晶格结构,需要更新更灵敏的非接触无损检测方法。
Dinwiddie等人采用红外相机揭示了增材制造过程中孔隙、未融合和外溅熔材等缺陷。他们开发的图像处理特殊算法可以定量描述孔隙率,但是没有具体说明可检测的最小缺陷尺寸。Gatto和Harris 用分辨率508像素/英寸的CMOS摄像头,安装在距离工作面135 mm的位置,在合成过程中,摄像头采取逐层拍照,然后通过专门开发的算法处理,获得各层几何参数,层照片可以确定孔隙的几何尺寸以及计算横截面的形状偏差等。这种方法的局限在于,一方面只能分析外部表面情况而无法检测内部,另一方面表面粗糙度会严重影响检测结果。
Guan等人采用EX1301迈克尔逊光学相干断层扫描系统评价选择性激光烧结的工件,其可以达到的三维图像的空间分辨率约为10 μm (相比之下X射线为50 μm),同时可以检测中空、未粘合和表面粗糙度,如图5所示,但是这种方法无法检测大尺寸工件。Guan等人指出,光波的穿透深度取决于材料的吸收和反射特性,并且背反射光波的空间相干性和时间相干性会影响测量精度,所以该技术只能应用于非金属材料。这种方法与X射线计算机断层扫描具有相同的灵敏度,但是光学层析技术可以用于逐层生长的过程检测。
Rudlin等人研究了涡流、激光超声、激光成像方法用于增材制造过程的检测。实际上,以上三种方法,都尚未用于制造过程的检测,仅能用于制备后的人工缺陷检测,评估增材制造工件的近表面缺陷。激光热成像的原理是采用红外相机针对样品中激光加热的部分进行实时热成像,揭示样品断面激光加热的不均匀性,该方法检测表面以下的缺陷时灵敏度低,试验中只可靠地检测了一个直径为0.6毫米深度为0.2毫米的缺陷。在0.5 mm以上的深度条件下,涡流技术的检测灵敏度为0.4 mm,而当检测近表面缺陷时,激光超声和激光成像方法的灵敏度要低于0.2 mm ,如图6所示。
激光超声检测是一种可用于快速扫描的非接触检测方法,利用超声在金相截面上横向和纵向的速度不同,可以表征样品中超声波传播的各向异性,若采用激光激励干涉接收,波前参数可用于确定近表面缺陷的尺寸和深度,通常用于焊缝的缺陷识别以确保管道和轨道的完整性,目前采用激光超声检查金属样品粉末沉积的研究还较少。由于激光超声可以采用一个激光源产生强大的超声波脉冲,具有易于支配的波形和宽光谱范围,因此与压电激励相比,其空间分辨率高3~10倍。同时,因为激光诱导超声脉冲不存在振荡,并且脉冲持续时间比PZT缩短6~7倍,因此可以实现更高的分辨率和更高的灵敏度,盲区很小。目前,激光超声对于尺寸范围150~500 μm的不连续缺陷,检测深度可达700 μm,但是当深度超过300 μm灵敏度明显减小,激光超声用于增材制造产品的孔隙率和各向异性检测的研究还很少。总之,激光超声用于增材制造的无损检测展现了较大的潜力,但还需要与制造过程进行集成,考虑使用这种方法对增材制造过程进行逐层实时监测。
此外,残余应力的测定方法可以分为物理测定法和机械测定法,机械测定法通常是破坏性方法,例如切槽法钻孔法。可用于残余应力检测的无损检测方法主要有磁性法、X射线衍射法及超声波法等。其中,磁性法是根据铁磁体饱和过程中应力与磁化曲线之间的变化关系进行测定,在一定范围内使用;X射线法理论完善,但存在射线伤害并且仅能测定表面应力及对特定位置的晶格畸变难以测量,因此其应用受到很大限制;超声波法则是无损检测方法中最有发展前景的方法,具有快速、现场实测方便、既能测表面又能测内部残余应力等特点,尤其是激光超声技术具有更大的应用潜力。
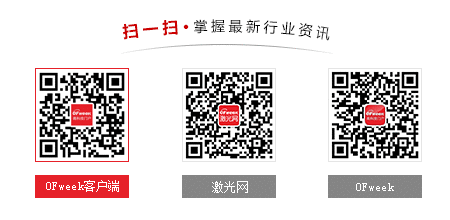
图片新闻
最新活动更多
-
5月22日立即报名>>> OFweek 2024新周期显示技术趋势研讨会
-
8月27-29日马上报名>>> 2024(第五届)全球数字经济产业大会暨展览会
-
8月27日立即报名>>> 2024先进激光技术博览展
-
精彩回顾立即查看>> 中科煜宸水导激光国产设备RJ305新品发布会
-
精彩回顾立即查看>> 2024激光行业应用创新发展蓝皮书火热招编中
-
精彩回顾立即查看>> 【线上直播】 2024世界激光产业大会
推荐专题
发表评论
请输入评论内容...
请输入评论/评论长度6~500个字
暂无评论
暂无评论