7.30-8.1 全数会2025(第六届)机器人及智能工厂展
火热报名中>>
相似和不同半导体材料的激光透射焊接
摘要:激光微焊接是一种应用于各个领域先进的制造方法。然而,到目前为止物理学限制阻碍了证明其在硅(Si)和其他技术必需的半导体材料中的适用性。针对强红外光作用下窄间隙材料界面可传递能量密度的光学限制,首次实现了用纳秒激光脉冲在Si工件间进行传输激光焊接的可行性论证。剪切连接强度为32±10 MPa,与复杂的替代工艺相比是非常有利的。在包括砷化镓在内的不同材料组合上及重复实验的支持下,证实了对于类似和不同的半导体都是可以实现的。演示依赖于小型光纤激光器,这一方面为高效灵活工艺的出现带来了巨大的希望,有利于包括片上实验室和混合半导体系统在内的重要技术发展。
1介绍
激光焊接是当今现代制造业的关键工艺。从这个观点出发,使用紧密聚焦的超短脉冲是一个重要的突破,它提供了在透明材料内部三维空间的任何地方通过非线性吸收来实现能量沉积的能力。随后高度局部化的材料熔化是飞秒激光焊接的基础。各种成功演示的应用包括穿过玻璃、穿过聚合物或穿过陶瓷的配置。虽然微键合肯定会在微电子学领域找到直接的应用,但令人惊讶的是,这种工艺不能直接适用于将不同的半导体工件键合在一起。如今,通过引入吸收层(如金属),用粘合剂来解决这个问题,从而导致解决方案与最苛刻的应用不兼容。
对于直接适用于硅(Si)和其他半导体的替代方法,可以参考晶圆分子键合。它包括适当地准备和放置两个晶圆在最亲密的接触,以便分子间的键出现在晶圆。然而,在通过热退火、表面等离子体活化或应用电场等工艺增强粘接之前,所得到的粘接强度仍然相对较低(几kPa)。这产生了典型的粘结强度,在几个MPa的顺序和性能水平适合一些高要求的应用。
然而,该技术的一个主要缺点是需要在洁净室环境中进行大量繁琐的步骤来组装功能性装置。在这种情况下,激光微焊接这种更直接的技术对于增加灵活性和制造当前方法无法实现的复杂结构半导体系统仍然是非常需要的。
2结果与讨论
2.1光接触的前提条件
为了证明激光焊接Si的可行性并揭示关键参数,我们使用掺铒光纤源在1550 nm波长发射持续时间< 5ns的脉冲,对两个相互堆叠的高纯度Si样品(双面抛光)之间的界面进行了辐照;这是硅的全透明域。利用前面提到的工作,证明了在紧聚焦条件下Si内部局部能量沉积的可能性,但也可能存在严重的非线性焦移,需要对加工区域定位进行预先补偿,我们首先集中在z-扫描程序上。实验方法如图1a所示。简而言之,它包括在0.45 NA(数值孔径)聚焦条件下,以最大可用能量(目标上11 μJ)和重复频率(1 kHz)重复1000次施加脉冲的单点照射。通过这种方式,我们产生了可以通过红外透射显微原位观察到的对比度良好的修饰。在图1b,c中,我们可以从侧面看到两个晶圆之间的界面附近。激光诱导的修饰以黑色细长标记(第一个修饰用向下的三角形表示)的形式横向分离,在两次照射之间以约12.5 μm的深度变化步距从上到下在界面上进行位移。在图1b中,当光束焦点向下z扫描(紫色虚线箭头)时,我们观察到所产生的修饰是如何通过界面复制的(红色虚线),并最终完全限制在较低的晶圆内。通过分离晶圆并通过可见显微镜观察接触的顶部和底部表面(图1d),我们在z扫描表面上识别出具有不对称的圆形特征,与延长的不对称修饰的横向观察相对应(图1b)。在这一阶段,在两种基材上获得的表面修饰(图1d)被视为一个令人惊喜的结果,因为它显示了在界面两侧一起加工材料的可能性。
图1:a)焊接结构示意图(z扫描和模式)和连续分离程序,以可视化激光照射时接触的顶部和底部晶圆表面的变化。b,c)两个Si晶片界面区域的红外透射显微镜横向视图。红色虚线表示接口的位置。在成像区中,从上到下不同深度(12.5 μm步长)(紫色虚线箭头)产生1000个11 μJ脉冲的单点修改(25 μm横向分离)。d,e)样品分离后顶部和底部晶圆表面对应的可见光显微镜图像,如(a)所示。界面下经过修饰的加工区域间接证明与底部晶圆具有良好的光学和高效耦合(b,d)。上样内部经过修饰的加工区域,横梁被界面反射,由于接触不完美而没有表面修饰(c,e)。
在样品的不同部分重复这个过程,我们意识到由于接触的不均匀性,它并不总是可重复的。这并不奇怪,因为任何激光焊接研究都表明,在加工过程中,理想情况下,材料应该紧密接触,以获得牢固可靠的粘结。在实践中,人们承认,间隙大于几微米的材料混合物是很难实现的。实现硅焊接的一个优势是微电子级晶圆的高规格,如用于这项工作的晶圆。亚纳米级的粗糙度和优秀的平整度(参见第4节关于样品的更多规格)非常有利于处理这一非平凡的力学问题,但它的高折射率(n = 3.5)导致任何接触缺陷都是谐振光学腔。在顶部和底部抛光晶圆之间存在小的空气间隙,可以引起几乎全反射,如图1c所示,在处理后的上部样品中可以看到明确的修改,并将光束初步聚焦在下片晶圆内部。考虑到这个光学问题,只有当间隙大大小于波长时,才会实现光学接触,光束可以轻松地通过界面而没有衰减(图1b)。对于较大的间隙,该接口充当了法布里-珀罗干涉仪的作用,对底部晶圆的传输受到限制(图1c)。考虑到硅的高折射率及其相关的高反射率(R≈30%),可以预测,这将成为比以前在玻璃或聚合物材料中的研究更为关键的方面。这些光学方面的考虑得到了图1e的证实,图1e显示,由于法布里-珀罗腔的适度局部传输,底部衬底表面完全没有修饰。更令人惊讶的特征是顶部晶圆表面也完全没有可见的修改,而横向视图清楚地显示顶部样品的一些内部修改被界面分割。与图1b,d相比,这表明两个表面上的电场显著减小,因此显然不适合焊接。
从这些初步观察中得出的一个主要结论是,为了初步实现类似半导体或其他高折射率材料的焊接,必须有近乎完美的光学接触。显然,这是一个与所需接触面积相关的非平凡问题。在接下来的研究中,我们依赖于典型的15 × 18 mm2表面积的高级抛光晶圆,并且系统地重复相同的制备程序,包括清洗步骤和对接触样品施加机械夹紧压力。正如我们稍后将看到的,尽管采用了这种程序,通过光束处理能力间接观察到的界面间隙仍然存在轻微的局部变化。然而,经过精心设计的测试和样品制备优化,这些不均匀性已大大减少。在这份专注于Si和GaAs的报告中,这些技术发展对于焊接性能的可重复性结果和可靠的统计分析至关重要。
2.2线形中证明材料混合
作为焊接的下一步,我们使用相同的辐照条件(0.45 NA, 11 μJ, 1 kHz),用重复脉冲产生连续的线形修饰。对于上述带有静态辐照和横向红外成像的z扫描方法,我们测试了相对于界面的不同焦移的响应。每条线长100 μm,是在光束以2 μm s-1的速度平行于界面平面的相对运动后得到的,根据我们的激光器的1 kHz重复频率,对应于施加的脉冲数≈7500,如图1d估计的修改尺寸≈15 μm。在图2a中,我们观察到分离后两种样品的光学显微镜图像。这导致了顶部和底部样本观测之间的镜像对称,如图1a所示。我们定义接口上最中心的修改所对应的位置z0作为比较的参考(基于图1b),我们在Si内部以12.5 μm的步长改变聚焦距离,在接口上方(正)和下方(负)(侧面视图红外图像显示在支持信息中)。在表面观察时,当光束聚焦在界面上方时,首先观察到宽度≈7 μm的细线。当我们向界面移动时,这些光束变得更宽(≈20 μm)和更暗,然后当光束聚焦在较低的晶圆内部时开始消失。至于静态情况下的光斑表面修改(图1d),在z扫描线中观察到的不对称性也与图1b中从横向视图中材料修改的横断面很好地对应。比较顶部和底部晶圆,我们可以观察到清晰的一对一的线轮廓映射,考虑到一个是另一个的镜像。这已经表明了由两个表面支持的改性体系,这是一个有利的观察,但并不能证明材料混合。
图2:a)相对于参考位置Z0在不同焦距下界面周围产生的线的顶部和底部晶片表面光学显微镜图像。b)相应的共聚焦显微图像显示表面形貌。顶部和底部线的轮廓和地形都相互匹配,表明晶圆之间有材料转移。注意图1a中所示的顶部和底部图像之间处理区域的镜像对应关系。
当我们用图2b所示的相应共聚焦显微镜图像分析表面形貌时,样品之间的物质转移变得明显。从这些图像中,我们观察到,不仅线条轮廓,而且两个晶圆上的地形轮廓都非常匹配,一个是另一个的负版本。微米尺寸的特征可以合理地作为加工区域中材料交换的证据,从而可能焊接,发现在参考位置(Z0)周围的聚焦条件下,材料转移最多。这已经代表了一个非常有希望的结果,清楚地表明了从简单的激光配置Si - Si微焊接的可行性,然而,在通过剪切连接强度测量评估之前,人们不能从它预先判断Si的粘合性能。
2.3粘结强度
为了进一步优化辐照条件,并在我们的配置中对最高可达到的键强进行测量,我们研究了施加脉冲数量的影响。为此,我们在相同的辐照条件(0.45 NA, 11 μJ, 1 kHz)下,以不同的扫描速度(1 μm s-1~ 5 mm s-1)制备了200 μm线。对于Si-Si配置,底部晶圆线光学图像的代表性选择如图3a所示。支持信息中给出了一套更完整的观察,包括对这种和其他测试材料组合的顶部晶圆表面的检查。正如人们所预期的那样,我们在Si-Si情况下观察到,在最低扫描速度下获得了最宽(≈15 μm)和最明显的标记,因此显示材料混合的最大加工体积,对应于最高的脉冲次数,因此培养效益最大。考虑到需要加工更大的区域以获得可测量的粘结强度,我们选择了2 μm s-1作为线质量和扫描速度之间的折衷。显然,这些最佳扫描条件直接取决于所使用的激光器的规格,为未来研究中使用提供更高功率和/或重复频率的光源进行进一步优化留下了空间。
图3:a) Si-Si和b) Si-GaAs结构底部晶片焊接线的光学显微镜图像。11 μJ下的最佳扫描条件分别为2 μm s-1和50 μm s-1。c)与(b)中图像相对应的共聚焦显微镜成像的地形图像。d)对应的测量区域(c)显示地表高程或凹陷超过固定在2 μm的阈值。e) Si-GaAs构型下焊接蛇纹石的红外透射图像。根据估算,约0.25mm2的总焊接面积应能抵抗高达4.5 N的剪切力。
在图3b中,展示了底部GaAs上产生的线的代表性图像选择。较低的修饰阈值使GaAs的相互作用更强,从而产生更宽(≈30μm)和更明显的线条。然而,与之前不同的是,对共焦图像的分析(图3c)揭示了最佳扫描速度,对应于50 μm s-1,而不是最慢的扫描速度。为了说明这方面的详细分析,我们在图3d中为图3c的每张图像展示了地形中海拔或凹陷超过2 μm的区域(|z|>2 μm)。将这一任意判据作为材料混合概率的评价标准,得出最佳扫描速度为50 μm s-1。与Si相比,这种增加的速度允许对几个样品进行更快的光栅扫描辐照(如图3e所示),从而在这种不同的半导体配置中测量到18±1 MPa的剪切连接强度。与Si-Si相比的差异可以合理地归因于与表现出不同热机械性能的材料焊接相关的通常挑战。然而,它是适合的而且测量的强度有趣地显示了这种技术的潜力,即使用贯穿Si传输配置将Si与其他半导体焊接。
对比图4中得到的剪切连接强度值,可以注意到这些值都在同一个数量级,其中Si-Si表现出最强的粘结。不同的材料焊接配置,无论是Si或GaAs在顶部,得到的值相似,都小于Si - Si得到的值。尽管对GaAs-GaAs焊接情况进行了一次测量,但结果表明Si-Si样品的性能水平(测量分布的底部),因此与类似半导体焊接所获得的优异性能一致。与此同时,有趣的是,与GaAs-Si相比,Si-GaAs结构中测量的统计色散有所减少。这表明GaAs对实验波动具有更好的鲁棒性,这也可以归因于GaAs的修饰阈值明显低于Si。考虑到这一点,我们假设Si - GaAs结构必须容忍更多的光学接触缺陷,即使在两个分离良好的表面(R = 30%)的预期界面透射率约为50%,在Si和GaAs低样品中,材料熔化也很容易同时达到。
图4:根据所有不同配置(如下所示)在焊接断裂前的剪切力测量(标记)来评估连接强度。每个构型的平均值用一条连续的直线表示。
3结论
这项工作证明了半导体激光焊接的可行性,使用非常紧凑的纳秒激光技术和相对松散的聚焦。在这方面,必须引入具有巨大应用潜力的解决方案。据我们所知,它不仅首次演示了类似半导体的激光焊接,而且还演示了不同半导体(Si和GaAs)的激光焊接。在所有配置中实现的键合强度都在数十兆帕左右,类似于通过晶圆键合技术和透明介质的超快激光焊接获得的键合强度,而这种技术不适用于具有常规激光加工配置的半导体。在这些比较的背景下,我们意识到,只有几毫米的焊缝与报告的强度必须悬挂激光设备,用于实现焊接。对于图5所示的性能的最后证据,使用Si-GaAs配置,因为它允许更高的处理速度。考虑到对接触不均匀性的剩余敏感性,这是一个与预期接触区域缩放的问题,我们有意地处理了一个相对较大的区域。如图5b所示,红外成像所示的总处理面积约为3.5 ×7.0 mm2,在此配置中测量的剪切连接强度为18 MPa(见图4),可抵抗高达400 N的剪切力,这比悬挂在激光头上所产生的约30 N的施加剪切力(≈3 kg)高出一个数量级。这些考虑解释了图5a所示的成功演示,尽管在图5b的红外传输图像中观察到不完全接触。
图5:a)实验中使用的激光源图像(≈3 kg)挂在焊接在GaAs上的Si晶片上。图示如图所示。b)从红外透射图像中,我们观察到总处理面积为3.5 ×7.0 mm2,从中我们估计对剪切力的阻力高达400 n。红外图像上可见的干涉条纹归因于材料界面处的法布里-珀罗腔,从而揭示了接触不均匀性。
为了扩展半导体焊接最合适的激光配置,我们的工作表明,鉴于半导体的窄带隙特性,除了在近红外或中红外要求适当的波长外,还必须特别注意两个关键方面, (i)第一个是对加工材料之间接近完美光学接触的要求,因为半导体固有的高折射率倾向于从界面中驱逐能量密度。如我们所示,这在相似的半导体焊接配置中尤其重要,而对于不同的半导体焊接,只要该工艺使用底部材料在所考虑的波长处吸收最大的配置,则可以允许更大的公差。(ii)第二个是关于用于能量传递的激光时间制度,因为总有一个不应超过的功率,以避免通量在到达界面之前发生剧烈的非线性离域。在这方面,我们可以强调使用超快激光技术进行透明材料焊接的巨大趋势。这在今天介质/槽介质中高度局部化和可控的能量沉积中是完全合理的。成功的玻璃-玻璃或玻璃-硅超快激光焊接演示,报告的剪切连接强度在某些情况下超过50兆帕,显然支持在这种情况下纳米秒激光焊接的优势。然而,这里值得强调的是,在IR域中类似的超短脉冲在半导体中完全失效。这是我们在实验中证实的一个方面(未显示),这与最近的文献一致,报告了强红外光在半导体内部由于强传播非线性而产生的强离域化。这一说法也与最近成功演示的皮秒激光脉冲硅铜焊接相一致,尽管采用了先进的非线性补偿措施,但与过去几十年广泛研究的穿玻璃超快激光焊接配置相比,焊接强度有限(最大剪切结合强度高达≈2 MPa)。
与目前应用于其他材料的晶圆键合和激光微焊接方法相比,我们的方法是一种非常经济和灵活的解决方案,因为它允许不同的材料组装,并且不需要洁净的环境。根据我们的演示,我们预计将根据目标应用程序快速获得各种改进。例如,使用高功率工业源,该过程将很容易扩大规模,以提高过程效率。从我们的方法中直接推断,几m s-1的扫描速度应该可以在MHz的重复频率和/或毫微米焦耳的能级下获得。总而言之,我们非常期待确定的纳秒激光解决方案,用于相似和不同半导体的微焊接,为半导体行业新的高价值制造实践打开了大门。
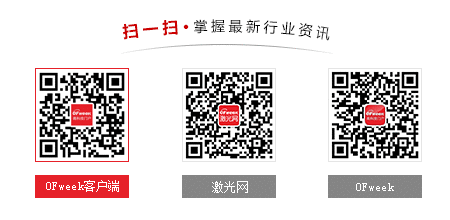
图片新闻
最新活动更多
-
7.30-8.1火热报名中>> 全数会2025(第六届)机器人及智能工厂展
-
7月30-31日报名参会>>> 全数会2025中国激光产业高质量发展峰会
-
7.30-8.1马上报名>>> 【展会】全数会 2025先进激光及工业光电展
-
免费参会立即报名>> 7月30日- 8月1日 2025全数会工业芯片与传感仪表展
-
精彩回顾立即查看>> 锐科激光《锐见·前沿》系列前沿激光应用工艺分享
-
精彩回顾立即查看>> 维度光电·引领光束质量分析应用全新浪潮【免费下载白皮书】
推荐专题
发表评论
请输入评论内容...
请输入评论/评论长度6~500个字
暂无评论
暂无评论