7.30-8.1 全数会2025(第六届)机器人及智能工厂展
火热报名中>>
激光粉末床熔合增材制造表面纹理与内部缺陷的相关性
摘要:在金属增材制造技术的实施过程中,现场监测和反馈控制系统的可用性确保了高质量的成品部件的制造。本研究旨在探讨激光粉末床熔合(LB - PBF)零件表面纹理与内部缺陷或密度之间的相关性。在本研究中,采用LB - PBF工艺对IN718镍合金粉末制备了120立方试样。根据ISO 25178 - 2标准确定了制造样品的密度和35个区域表面纹理参数。采用统计学方法,观察到试样表面纹理参数与密度或内部缺陷之间有很强的相关性。特别是,面积表面纹理参数,如缩小谷高度、岩心高度、均方根高度和均方根梯度,与样品密度有很强的相关性。因此,对这些区域表面纹理参数进行现场监测,有助于将其作为反馈系统的控制变量。
介绍:
金属增材制造(AM),特别是粉末床熔合(PBF)被认为是制造新材料的重要工艺,具有优异的材料性能和复杂的结构。这个过程涉及到使用激光或电子束作为热源。然而,人们对使用PBF工艺获得的成品零件的质量提出了一些担忧。这些问题涉及到成品零件中气孔和缺乏融合等缺陷的出现,以及由于PBF工艺固有的特性而在加工过程中表面粗糙度的恶化。因此,发现PBF制造的零件的机械性能和表面粗糙度低于锻造材料。因此,在PBF加工过程中尽量减少缺陷的发生并确保成品零件的高质量的需求导致了监测和反馈控制系统的发展。
为了该系统的发展,阐明激光-PBF过程中发生的物理现象是非常重要的。粉末特性影响其重涂,从而影响激光照射引起的熔化和凝固现象,进而影响成品零件的质量。现有研究了熔池行为以及缺陷发生的原因,如气孔和缺乏融合,不仅通过使用试验台和高速摄像机进行实验,而且还通过数值模拟。通过监测熔池的结构和温度等熔池状态参数来控制激光辐射水平。其他先前的研究通过使用装有1千瓦大功率单模光纤激光器、高速摄像机和热观察器的试验台进行实验,研究了识别熔化和凝固现象的方法。在这些现有的研究中也进行了数值模拟。
此外,Calta 等人和Martin等人利用原位时间分辨x射线成像和衍射分析研究了锁孔和孔隙的形成现象。Zhao等人和Cunningham等人利用超高速同步加速器x射线成像研究了锁孔的形成和溅射。
成品零件的质量要求包括满足标准化机械性能要求、表面粗糙度标准和精度。这些性能受到激光辐射引起的熔化和凝固现象的影响。因此,熔炼和凝固过程中内部缺陷的发生和表面粗糙度的不一致被认为会影响成品零件的质量。工艺参数对内部缺陷发生和/或成品零件密度的影响已被频繁报道。因此,激光功率、扫描速度、孵化间距和层厚被确定为LB-PBF-LB的基本工艺参数。激光功率和扫描速度工艺图用于确定最佳工艺参数。Aoyagi等人利用支持向量机构建了电子束PBF (EPBF)工艺流程图。Gobert等人在PBF过程中使用监督机器学习进行缺陷检测。此外,由于体积能量密度(能量密度)与成品零件的缺陷和密度有很强的相关性,因此被广泛采用为工艺参数。
结果与讨论
工艺参数与密度的关系
在本研究中进行的实验包括制造尺寸为10 × 10 × 10 mm的铬镍铁合金718 (IN 718)立方样品(图1A)。样品制作采用PBF试验台,配有1 kw单模光纤激光器,在氮气环境(含氧量< 0.1 wt%)下进行。制备过程中还考虑了激光光斑直径d = 100μm (1/e2)、激光功率P = 175-800 W、扫描速度v = 550-2850 mm/s、孵化间距h = 0.10 mm、层厚t = 0.05 mm、能量密度E = 24.1-82.4 J/mm3等操作条件。能量密度E由关系式E=P/vht计算。因此,在宽范围的激光功率(高达800 W)和扫描速度(高达2850 mm/s)值下,研究了工艺参数和密度之间的关系,这大大超过了现有研究报告的结果。
图1:用相对密度评价工艺参数与密度之间的关系,(A)立方试样;(B)激光功率与扫描速度之间的流程图;(C)相对密度与能量密度的关系。
使用本研究中制备的120立方样品的相对密度值评估激光功率与扫描速度的过程图如图1B所示。相对密度由建成试件的阿基米德原理密度除以其对应的真实密度(8.20 g/cm3)计算。图1B中低功率和低扫描速度区域对应的高相对密度值超过99.7%。同时,高功率(超过400w)和高扫描速度(超过2000mm /s)的区域是低相对密度的代表。正如先前的一项研究所报道的那样,观察到的密度降低可以归因于熔池不稳定和强烈飞溅引起的缺乏融合。此外,使用高激光功率会导致小孔气孔的产生。在高激光功率和高扫描速度下发生的熔化和凝固现象在以往的研究中很少报道。相反,试样密度的降低是一种常见的观察结果,表明考虑了不利的制造条件,包括使用低功率和低扫描速度。
所制备立方试样的能量密度与相对密度之间的关系如图1C所示。相对密度随着能量密度的增加而增加,并达到其最大值(称为“全密度”),对应于大约35 J/mm3的能量密度值。在其他材料中也可以观察到类似的趋势,尽管这不仅取决于材料,还取决于粉末和激光特性。虽然大多数情况下,包括400w激光功率对应的情况,都遵循这一趋势,但很少有情况不符合这一趋势。这些偏离情况对应于使用高激光功率(超过400w)和高扫描速度(2000mm /s)的情况。收集数据的差异可以归因于先前报道的由于熔池不稳定而产生的强烈飞溅,以及Zhao等人和Cunningham等人报道的在高功率和扫描速度下产生的残余锁孔孔隙。
图2为高、低密度立方试样的扫描电子显微镜(SEM)和x射线计算机断层扫描(XCT)图像;这些图像分别使用JEOL JSM-7800F和尼康XT H225ST拍摄。利用43.5 J/ mm3的能量密度制备的全密度试样(XCT-1)的SEM和XCT图像显示,很少有直径小于10微米的微孔(图2A, C, E)。同时,以29 J/ mm3的低能量密度制备的98%相对密度试样(XCT)的SEM和XCT图像显示,大量的未融合缺陷(图2B, D, F)。
图2:立方试样内部缺陷的观察- (A, C, E) X-CT1图像E = 43.5 J/ mm3, D = 100.1%(B, D, F) X-CT2图像与E = 29.0 J / mm3 D = 98.3%。(A)和(B)为立方试样截面的扫描电镜图像;(C)和(D)为三维XCT图像;(E)和(F)为二维XCT图像。(G) D = 99.7%的图像。
因此,在扫描速度为2000 mm/s、能量密度超过35 J/ mm3、激光功率小于500 w的情况下,可以制备出接近真实密度的样品。此外,相对密度超过99.7%的试样的结构特征是存在直径小于~ 10μm的微孔(图2G)。这对LB-PBF IN718的疲劳强度没有显著影响。因此,我们将99.7%的相对密度作为阈值。
S1-S9标本(图1B, C)的光学显微镜(OM)图像如图3所示。可以看出,全密度试件s7、S8和S9中缺陷很少。同时,相对密度为99%的样品S4存在少量孔隙,而相对密度较低的样品S1、S2和S3存在未融合缺陷和孔隙。因此,在相对密度值低于99%左右的材料中容易出现未融合缺陷。因此,随着材料相对密度的降低,这些缺陷变得更加突出。
图3:试件(s1 ~ s9)截面OM图像。
在使用高激光功率的制备条件下,微孔以小孔或气孔的形式存在,并伴有缺乏融合的缺陷,如图3中试件S1和试件S3所示。Cunningham等人使用Ti - 6AI - 4V合金的工艺图,阐明了锁孔配置和工艺参数(激光功率和扫描速度)之间的关系,激光功率和扫描速度分别高达500 W和1200 mm/s。正如Martin等人所报道的那样,由于激光功率增加,锁眼深度增加,因此锁眼孔孔倾向于保持在锁眼底部。图1B所示的工艺图分析显示,在高相对密度(> 99.7%)区域存在微孔,但没有任何缺乏融合缺陷。然而,在该区域之外,缺乏融合缺陷和微孔的出现显著增加。因此,在高功率和高扫描速度条件下制备的低密度试样(S1和S3)区域存在几个未融合缺陷。这证实了内部缺陷的形态,如缺乏融合和微孔的形成,与试样密度有很强的相关性。
表面纹理与内部缺陷的关系
图1B对应的工艺示意图叠加S1-S16试样的表面织构和内部缺陷如图4A所示。从图中可以看出,对于高密度试样S15和S16,迹线(熔池迹线)的宽度保持相对恒定,迹线之间没有沟槽。如前所述,全密度样品中存在可忽略不计的孔隙。而在低密度试样S10、S12和S13中,该轨迹宽度仍然不规则,且表面含有若干凸起和凹槽。因此,在较低的激光功率下观察到较宽的沟槽,并且激光功率的增加增加了轨道的宽度和不均匀性。此外,尽管密度与S10相似,但使用最高激光功率(600 W)制备的试样S11表面具有更宽的轨道和凹槽以及更大的轨道不均匀性。这可以归因于在高能量密度下瑞利高原毛细不稳定性引起熔池的大膨胀(“珠状”)。因此,在这些样品中出现了缺乏融合的缺陷和孔隙。
图4:表面纹理和内部缺陷之间的关系- (A)激光功率和扫描速度之间基于相对密度的过程映射,包括表面纹理和内部缺陷图像;(B)立方试样(S10-S16)表面SEM和CSI图像;(C)表面纹理评估区。
图5:样品在低功率和低扫描速度区域的CSI图像。
因此,可以推断,加工样品的材料密度和内部缺陷与其表面织构密切相关。因此,量化了所有立方试样的面表面纹理参数,并研究了它们与材料密度的相关性,将这些参数应用于监测和反馈系统。
Whip等人已经证实了应用ISO 25178 - 2区域表面纹理参数来描述AM零件表面粗糙度的充分性。此外,Gomez等人报道了CSI技术为具有不同粗糙度水平和坡度分布的金属AM表面提供了优异的表面形貌测量结果。据此,本研究采用CSI仪器(Zygo newview9000)测定了制备试样的ISO25178-6区域表面织构参数。用1 ×变焦和10 ×物镜组合测量。采样间隔设置为0.86μm。视场测量为1.37 × 1.03 mm, 10 × 10 mm表面积的测量是通过大约25%重叠的拼接进行的。在整个10 × 10 mm表面上分析了120个试样的表面纹理。然而,由于壁效应导致试样近边缘区域膨胀,只能提取中心6 × 6表面(图4C)的数据进行分析。
样品S10-S16的CSI和表面SEM图像如图4B所示。如上所述,参考图4A表明,由于熔池行为和飞溅的变化,制备样品的表面纹理与工艺参数密切相关。在低功率和低扫描速度条件下制备的样品CSI图像如图5所示。在激光功率一定时,表面粗糙度随扫描速度的增加而增大。这种不均匀性可以在低密度试样的整个表面观察到。同时,在一定扫描速度下,由于熔池宽度和不稳定性的增加,表面不均匀度随着激光功率的增加而增加。与图4B所示的扫描电镜图像中所示的表面相比,图5中的低密度试样表面表现出更严重的不均匀性,这是由于轨道之间出现了沟槽。缺乏融合缺陷和飞溅。相比之下,在中等密度(99-99.7%)的试样表面可见的缺陷较少。相应的,全密度试样由于形成规则的轨迹和低溅射计数,表面纹理保持均匀。因此,CSI图像与SEM结果具有很强的一致性,可以用来评价加工样品的表面纹理。这表明,利用样品表面的CSI图像可以预测样品的材料密度或内部缺陷状态。
利用面表面纹理参数预测材料密度和缺陷
先前研究了CSI图像,证明了工艺参数对材料表面纹理的影响。然而,正如前面所讨论的,工艺参数和表面纹理之间的关系是复杂的。虽然已有研究研究了表面织构与材料密度之间的相关性,但表面织构参数与密度或内部缺陷之间的相关性尚未定量研究。
在基于CSI的表面纹理评估中,由于激光反射不足,难以对具有挑战的和复杂粗糙特征的表面进行可靠的测量。如前所述,由于试样表面在某些制造条件下由于飞溅和不稳定的轨迹形成而显示出复杂的粗糙,因此由于未测量数据,表面纹理参数的值预计会显示出较大的变化。在高激光功率下加工的样品,未测量数据的百分比(黑色区域)明显增加,如图(补充图1)所示。此外,我们知道,在高激光功率和高扫描速度下,由于出现了钥匙孔和珠状凸起,零件的密度下降。如图1B所示,当激光功率大于400 W时,试样的密度较低。因此,在400w及以下激光功率下制备的88个样品进行了表面织构评价。
A
B
补充图1:由于激光反射不足(黑色区域),表面具有陡坡和复杂粗糙特征的样品的例子。(A)在高激光功率和高扫描速度下制备S1试样。(B)在低激光功率和低扫描速度下制备的S15样品。
在对88个试样的表面纹理参数进行评估后,利用实测数据计算了ISO 25178 - 2标准中规定的35个区域表面纹理参数。由于表面纹理与试样密度具有很强的相关性,因此采用最大信息系数(MIC)进行了非线性相关分析。得到的面表面纹理参数与立方试样相对密度之间的相关性如图6所示。地形高度分布参数相关系数的对应值。偏度Ssk和峰度sku分别为0.42和0.34。偏度Ssk是测量表面偏差在平均平面周围的不对称性,峰度Sku是测量表面高度分布的峰度或锐度。这些参数与样品密度呈弱相关关系。基于高度的参数最大高度Sz和最大坑高sv的相关系数分别为0.71和0.55。由此可见,Sv与试件密度的相关性较弱,而Sz与试件密度的相关性较强。同时,河谷高度Svk降低后MIC值最高,为0.81,而核心高度Sk、均方根高度Sq和均方根梯度Sdq分别为0.78、0.76和0.76。根据46,MIC值超过0.8意味着两个变量之间的相关性极强。由此可见,区域表面纹理参数Svk、Sk、Sq和Sdq与样品密度密切相关。
图6:35个区域表面纹理参数与120立方样品相对密度的相关性。
特别是,通过测量岩心粗糙度以下的山谷深度,得到的减小的山谷深度Svk与样品密度有很强的相关性。根据ISO25178-2标准的定义,它可以计算为直角三角形的高度,该直角三角形的面积等于从核心表面突出的山谷区域。这意味着在面积物质比曲线中心区域的等效直线(即Svk)的梯度随着表面粗糙度高度差和山谷体积的增加而增加。因此,使用Svk可以有效地评估样品表面纹理与相对较大缺陷(如缺乏融合)之间的相关性。
因此,具有高相关系数的地形高度分布参数svk、Sk、Sq和sdq可以有效地评价成品件的密度相关性。通过使用相对密度和减小的河谷高度(Svk)评估的过程图之间的相似性验证了这一推断,如补充图2所示。
补充图2:在低功耗和低扫描速度区域,使用(a)相对密度,(b)缩小谷高度(Svk),(c)核心高度(Sk), (d)均方根高度(Sq)和(e)均方根梯度(Sdq)评估的过程图之间的比较。
总之,该研究揭示了面表面纹理参数的存在,特别是Svk, Sk, Sq和Sdq,这些参数与lb - pbf制造样品的密度或内部缺陷密切相关。这一发现使得使用原位表面纹理监测标本来预测其密度或其结构中的内部缺陷成为可能。为此,可以设置区域表面纹理参数svk、Sk、Sq或sdq的阈值。此外,对这些参数值的现场监测可用于实现反馈控制,从而通过消除缺陷产生来生产稳定的高质量零件。
材料与方法
材料
在本研究中,采用气雾化Inconel 718 (IN718)粉末(LPW技术)。SEM图像见补充图3。平均直径(D50)为29.61 μ m。霍尔流量计漏斗流速(s/50 g)为15.28 s,休止角为28°。
补充图3:IN718粉末的SEM图像。
LB-PBF试验台
LB-PBF试验台由一台1kw单模光纤激光器和一台电流激光扫描仪组成。光纤激光波长为1070 nm,激光直径为100μm (1/e2)。建筑体积直径为150毫米,深度为150毫米。试验台配有熔池和表面形貌监测系统。样品在含氧< 0.1 wt%的氮气环境中制备。
相干扫描成像
采用CSI系统(ZYGO NewView?9000 CSI系统)测量试样的ISO25178-6区域表面纹理参数(补充表1)。用1 ×变焦和10 ×物镜组合测量。采样间隔设置为0.86μm。测量的视场为1.37 ×1.03 mm, 10 × 10 mm表面积的测量是通过重叠约25%的拼接获得的。CSI图像和实测数据示例见补充图4。
补充图4:使用相干扫描系统测量的SCI图像示例。
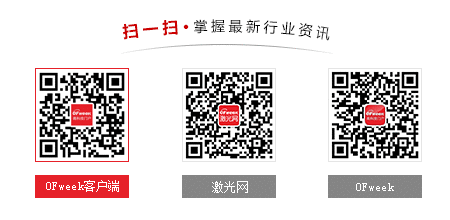
图片新闻
最新活动更多
-
7.30-8.1火热报名中>> 全数会2025(第六届)机器人及智能工厂展
-
7月30-31日报名参会>>> 全数会2025中国激光产业高质量发展峰会
-
7.30-8.1马上报名>>> 【展会】全数会 2025先进激光及工业光电展
-
免费参会立即报名>> 7月30日- 8月1日 2025全数会工业芯片与传感仪表展
-
精彩回顾立即查看>> 锐科激光《锐见·前沿》系列前沿激光应用工艺分享
-
精彩回顾立即查看>> 维度光电·引领光束质量分析应用全新浪潮【免费下载白皮书】
推荐专题
-
5 智驾没有理想主义
发表评论
请输入评论内容...
请输入评论/评论长度6~500个字
暂无评论
暂无评论