7.30-8.1 全数会2025(第六届)机器人及智能工厂展
火热报名中>>
国务院节能环保产业发展意见使激光迎来发展机遇
存在的挑战
虽然激光焊接非常适用于生产电池组,但应用于这一产业仍存在挑战。
成功的激光焊接要求被焊基材之间紧密接触。这需要仔细紧固零件,以取得最佳效果。而这在纤薄的极耳基材上很难做好,因为它容易弯曲失准,特别是在极耳嵌入大型电池模块或组件的情况下。
电池组装行业希望利用现有的焊接设备来收集加工数据,以跟踪焊接工艺,实现质量控制。超声波和电阻焊接设备目前已能提供这信息。另一方面,激光系统是定制的激光器、光学器件和运动控制系统的组合,专为某种应用量身定制。目前尚没有现成的设计用于电池极耳组装的激光焊接系统,能够提供加工监控信息以确保焊接质量和可靠性。
最后, 要注意激光焊接是一个熔化过程。这意味着两个基底在激光焊接过程中会熔化。这一过程很快,因此整个热输入较低。但因为这是一个熔化过程,在焊接不同材料的时候就可能形成易碎的高电阻金属间化合物。铝-铜组合特别容易形成金属间化合物。这些化合物已证明对于微电子设备搭接头的短期电气性能和长期机械性能有负面影响。这些金属间化合物对于锂电池长期性能的影响尚不确定。
激光焊接是组装电池组件时搭接电池极耳的明智选择。该工艺极为迅速高效,并为所有材料组合提供高强度的焊接。这一工艺容易适用于多种搭接头设计。与超声波焊、电阻焊相比,激光焊接铝、铜和镍同类材质时具有更好的抗剪切和抗撕强度。激光焊接应用于连接铝和铝以及铜和铜材料时尤为成功。如果集成商能够为电池/电池组制造商开发出现成的系统,激光焊接就能够和其它用于电动汽车电池组、电池块组装市场的现有技术相抗衡。
2、锂电池检测将采用激光测量技术
传统锂电池高度的检测方式一般是人工使用卡尺进行测量,受电池边缘焊接影响,会降低人工检测的准确度,且人工卡尺检测本身就存在检测数据不准确的情况,这就造成了工厂最大的困扰--尺寸检测数据不准确。
工厂电池检测数量大,在检测过程中人工参与判断,检测失误后很难追本溯源,给公司产品质量带来的负面影响不可估量。因此,锂电池测量数据不准确、人工判断失误、情绪失控等众多主客观因素,将严重影响锂电池的交付质量。目前,锂电池高度测量在自动检测领域还几乎是一片空白。
如果采用先进的激光测试技术,选用两个激光器进行高度测量,通过电池和激光器间的相对位移,实现对电池两端进行轮廓扫描,用自主研发的测试分析软件对高度值进行提取,并计算高度差。每分钟可检测40块锂电池,测试精度达到0.02mm,检测电池尺寸覆盖范围广:宽度25~80mm,厚度3.0~15mm,高度30~100mm。
该系统运用非接触式光学测量,快速检测多种锂电池产品的高度和高度差,并进行自动分选。人工上料到物料盒进行检测,检测后的电池分为合格品和不合格品,并对其分类输出。该设备具有检测数据自动存储功能,统计每批产品合格率等数据,自动生成报表,方便对产品质量的追溯和控制。
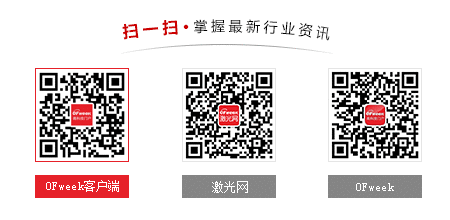
图片新闻
最新活动更多
-
7.30-8.1火热报名中>> 全数会2025(第六届)机器人及智能工厂展
-
7月30-31日报名参会>>> 全数会2025中国激光产业高质量发展峰会
-
7.30-8.1马上报名>>> 【展会】全数会 2025先进激光及工业光电展
-
免费参会立即报名>> 7月30日- 8月1日 2025全数会工业芯片与传感仪表展
-
精彩回顾立即查看>> 锐科激光《锐见·前沿》系列前沿激光应用工艺分享
-
精彩回顾立即查看>> 维度光电·引领光束质量分析应用全新浪潮【免费下载白皮书】
推荐专题
发表评论
请输入评论内容...
请输入评论/评论长度6~500个字
暂无评论
暂无评论